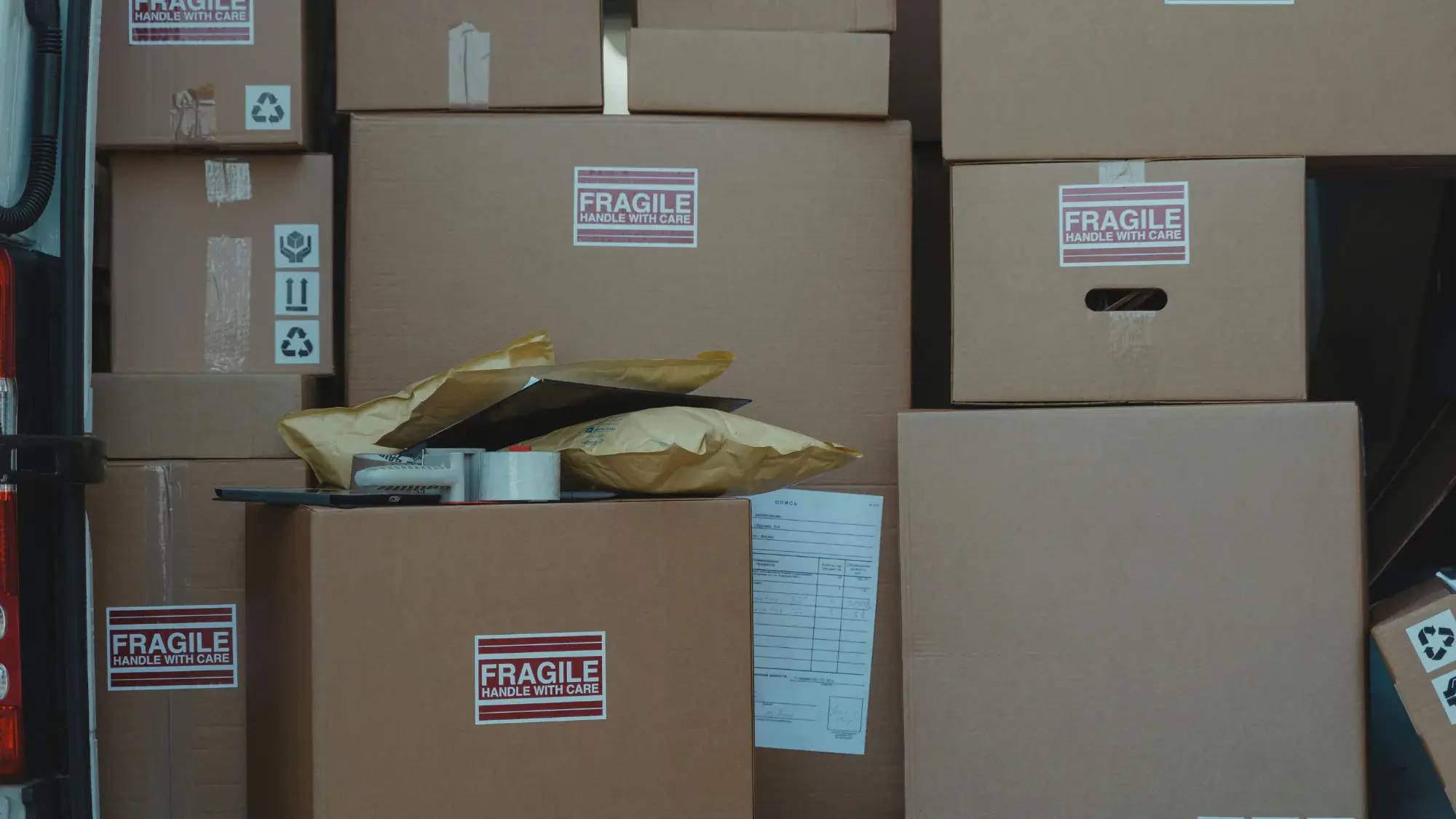
Imagine this: a truckload of critical components destined for a major manufacturing plant sits idle at a warehouse. Why? Because the freight was misclassified, leading to unexpected charges and a costly delay. Or picture a shipment of delicate electronics arriving at its destination, only to find the goods damaged due to improper packaging.
Unfortunately, these scenarios are all too common in the world of freight shipping. Navigating the complexities of logistics can be a minefield of potential pitfalls. Avoiding these common mistakes is the key to maintaining efficiency in your supply chain, controlling costs, and, most importantly, ensuring customer satisfaction.
In this post, we'll explore some of the most frequent freight shipping errors businesses make, and, more importantly, we'll provide actionable strategies to avoid them. Let's start with the first, and perhaps most costly, mistake: misclassifying your freight.
Mistake #1: Misclassifying LTL Freight
Freight classification is a standardized system that categorizes shipments based on their characteristics. This system is essential because it determines the rate a carrier charges for transporting the freight. The National Motor Freight Classification (NMFC) system, maintained by the National Motor Freight Traffic Association (NMFTA), assigns a specific code to virtually every type of commodity. These codes range from 50 (least dense, most expensive to ship) to 500 (most dense, least expensive to ship). Factors like density, weight, value, and handling characteristics all play a role in determining the appropriate freight class.
Misclassifying your freight, whether intentionally or accidentally, can have significant consequences. One of the most common is unexpected charges. If you declare a lower freight class than is actually applicable, the carrier will likely reclassify the shipment and bill you the difference, often with added fees. This can throw your budget off and lead to disputes. Misclassification can also cause delays. Carriers may hold shipments until the classification issue is resolved, disrupting your supply chain and potentially impacting delivery deadlines. In some cases, misclassified shipments may even be rejected outright, forcing you to start the shipping process all over again.
Mastering Freight Classification
So, how can you avoid this costly mistake? First, understand the factors that determine freight class. Density, which is the weight of the shipment divided by its volume, is a primary factor. Heavier and more compact shipments generally fall into lower, less expensive classes. Value also plays a role. High-value items are often assigned higher classes due to the increased risk of loss or damage. Similarly, items that are fragile, hazardous, or require special handling will also be assigned higher classes.
To accurately determine your freight class, consult the NMFC directory. The NMFTA website offers resources and tools to help you understand NMFC codes. When in doubt, it's always best to err on the side of caution and classify your freight slightly higher rather than lower. Finally, double-check your classifications before tendering your shipment to the carrier. A few minutes of careful review can save you time, money, and headaches in the long run.
Psst: There are new updates to NMFC Classification in 2025. Check out our ebook and make sure you're prepared.
Mistake #2: Inadequate Packaging
Inadequate packaging is another common culprit behind freight shipping woes. From crushed boxes to shattered goods, the consequences of improper packaging can be devastating. Damaged goods, of course, lead to financial losses, customer dissatisfaction, and time-consuming claims processes. In some cases, inadequate packaging can even result in lost items, especially if labels become detached or illegible. The impact extends beyond just the immediate shipment. Increased claims can lead to higher insurance premiums and damage your company's reputation.
Think of a shipment of ceramic tiles packed loosely in a cardboard box with minimal cushioning. It's easy to imagine the damage that could occur during transit. Or picture a pallet of canned goods wrapped in a single layer of shrink wrap. The weight of the load could easily cause the wrap to tear, leading to scattered cans and potential damage.
Protecting Your Investment
So, how can you ensure your goods arrive at their destination safe and sound? First, consider the nature of your freight. Fragile items require more protection than durable goods. Use appropriate packing materials, such as foam, bubble wrap, or packing peanuts, to cushion and protect your items. For heavier shipments, pallets and crates provide a sturdy base and prevent shifting during transit. Securely fasten your goods to the pallet or crate using straps or shrink wrap. When using shrink wrap, apply multiple layers for added strength and stability.
Labeling is just as important as the packaging itself. Clearly and correctly label each package with the recipient's address, contact information, and any special handling instructions. Use large, easy-to-read font, and consider using multiple labels to ensure visibility. For international shipments, include all necessary customs documentation.
Mistake #3: Poor Communication
Effective communication is the lifeblood of successful freight shipping. Conversely, breakdowns in communication can lead to a cascade of problems, from frustrating delays to costly errors.
When information is unclear, incomplete, or simply not shared, the entire shipping process can grind to a halt. Missed pickups, for example, often occur because the carrier wasn't properly informed of the pickup location or schedule. Incorrect delivery instructions can result in shipments being delivered to the wrong address, leading to further delays and added expenses. A lack of updates on the status of a shipment can leave both the shipper and the receiver in the dark, creating uncertainty and frustration.
Effective Communication Strategies
So, how can you foster clear and consistent communication throughout the shipping process? First, recognize that communication is a two-way street. All parties involved–the shipper, the carrier, and the receiver–must be proactive in sharing information. Use clear and concise language, avoiding jargon or technical terms that may not be universally understood.
Technology plays a crucial role in facilitating communication. Utilize tools that provide real-time tracking and updates on the location and status of your shipments. This allows you to anticipate potential delays and proactively communicate with your customers. Don't wait for problems to arise; be proactive in your communication. Regularly check in with your carrier and keep your receiver informed of any changes or updates to minimize the risk of errors, delays, and frustration in your freight shipping operations.
Mistake #4: Ignoring Transit Time and Delivery Schedules
Unrealistic expectations about transit times and delivery schedules can wreak havoc on supply chains, leading to production delays, stockouts, and dissatisfied customers. Imagine a manufacturer relying on just-in-time delivery of raw materials, only to have their shipment delayed due to unforeseen circumstances. The entire production process could grind to a halt, resulting in significant financial losses. Similarly, promising a customer a delivery date that is simply not achievable can damage your reputation and lead to lost business.
Several factors can affect transit times, including weather conditions, traffic congestion, the distance the shipment needs to travel, and the carrier's schedules. A severe snowstorm, for example, can cause significant delays in ground transportation. Unexpected traffic incidents can also disrupt delivery schedules. Of course, the longer the distance, the more time it will generally take for a shipment to arrive. And finally, carriers have their own schedules and routes, which can impact delivery times.
Optimizing Delivery Schedules
So, how can you avoid the pitfalls of unrealistic transit time expectations? First, when planning your shipments, always factor in potential delays. Don't assume that everything will go perfectly. Build in some buffer time to account for unforeseen circumstances. Utilize tracking tools to monitor your shipments in transit. This will allow you to identify potential delays early on and take corrective action if necessary.
Most importantly, communicate realistic delivery windows to your customers. It's always better to under-promise and over-deliver than to over-promise and under-deliver. By setting realistic expectations, you can maintain customer satisfaction and avoid the disruptions caused by missed deadlines.
The Path to Smoother Shipping
From misclassifying freight and inadequate packaging to poor communication and a lack of understanding of Incoterms, the world of freight shipping is rife with potential pitfalls. These common mistakes can lead to unexpected costs, frustrating delays, and damaged goods, ultimately impacting your bottom line and customer satisfaction. But as we've seen, many of these issues can be avoided with proactive planning, clear communication, and a solid understanding of the intricacies of freight logistics.
Navigating these complexities can be challenging, but it doesn't have to be. Customodal is here to help businesses like yours streamline shipping processes and optimize their strategies. Our expertise and extensive network of carriers allow us to handle the details so you can focus on what you do best.
Contact Customodal today for a consultation and discover how we can help you avoid costly mistakes and take your freight shipping to the next level.