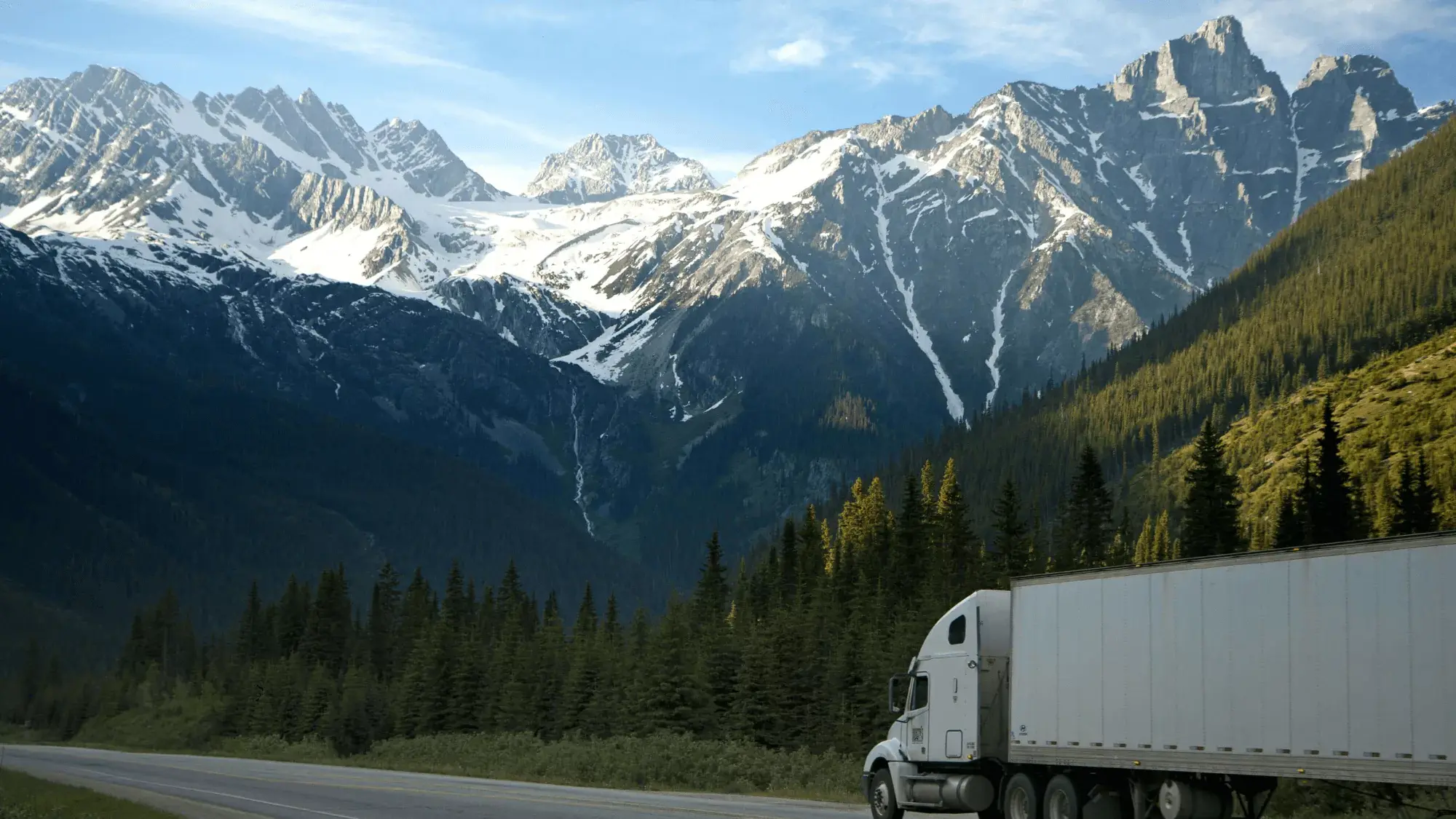
Outbound freight logistics–the process of getting your product into the customer's hands – is facing unprecedented challenges. Disruptions are more frequent, capacity is tighter than ever, and the regulatory landscape grows increasingly complex. These factors can easily lead to costly delays and dissatisfied customers.
Imagine a manufacturer relying on a single trucking company during a sudden surge in demand; what happens if that carrier can't handle the volume? That's why having the right logistics solutions in place is crucial to navigate these obstacles and ensure your goods reach their destination efficiently and on time.
1. Capacity Crunches and Carrier Selection
Capacity crunches are a recurring headache in the freight industry. Essentially, it's when there aren't enough trucks or shipping containers available to meet demand. This can happen for a variety of reasons, from predictable seasonal peaks–like the holiday shopping rush–to unexpected disruptions, such as a major port closure due to a hurricane. When capacity tightens, shippers face delays, higher transportation costs, and potential damage to their customer relationships.
In 2023, 63% of shippers experienced an increase in tender rejection rates, indicating a tight-capacity environment.
Diversity Your Carrier Mix
To avoid getting squeezed, it's crucial to diversify your carrier mix. Instead of relying solely on one trucking company or shipping line, build relationships with a portfolio of carriers. This strategy offers several advantages. First, it provides flexibility. If one carrier experiences operational issues or lacks capacity, you have backup options. Second, different carriers have different strengths. Some might specialize in certain regions or types of cargo, while others excel at expedited shipping.
By strategically selecting your carrier mix, you can ensure access to the right equipment and expertise for your specific needs. For instance, if a company relies solely on a carrier specializing in long-haul trucking and suddenly needs to move a small, urgent shipment to a nearby city, they may face delays and higher costs. Having a local carrier in their network would solve this problem.
2. Bridging the Communication Gap
Clear communication is the lifeblood of efficient outbound freight logistics. Yet, with multiple parties involved–manufacturers, carriers, third-party logistics providers, and customers – miscommunications are a common occurrence. These breakdowns can lead to costly mistakes, delays, and damaged relationships. It's like a game of telephone, where the message gets distorted with each handoff.
43% of supply chain professionals cite poor communication as a major obstacle to efficient logistics.
One crucial factor in effective communication is "translating" between different stakeholders. Manufacturers often use technical jargon and internal codes that are unfamiliar to carriers. Conversely, drivers and dispatchers may use trucking-specific terminology that confuses those outside the industry. For instance, a manufacturer might refer to a product by its internal SKU, while the carrier needs the proper shipping name and hazardous materials classification (if applicable) to transport it safely and compliantly.
One example of this would be when a shipper schedules a truck and orders a "van." In the trucking world, "van" typically refers to a 53-foot semi-trailer. If the shipper actually needs a smaller sprinter van, they might be surprised when a large semi-truck arrives for pickup.
Speak the Same "Language"
If those involved in the shipping process aren't "speaking the same language," so to speak, crucial messages may get lost in translation. This disconnect can lead to confusion, delays, and even safety hazards.
To avoid these pitfalls, it's essential to use clear, concise language that everyone understands. Avoid jargon and acronyms whenever possible, and provide detailed explanations when necessary. Think of it as translating between two languages–the language of manufacturing and the language of transportation.
Establish Communication Channels
Beyond terminology, establishing clear and consistent communication channels is paramount. Everyone involved in the shipment must be on the same page, from pick-up to final delivery. This starts with using standardized documentation. For instance, using clear and consistent product descriptions, packaging specifications, and delivery instructions minimizes the risk of misinterpretation.
Leverage Real-Time Technology
Technology also plays a vital role in bridging the communication gap. Real-time information-sharing platforms, such as Transportation Management Systems (TMS), allow all stakeholders to track shipments, exchange updates, and address potential issues proactively. A TMS can provide instant notifications about schedule changes, delays, or delivery confirmations, keeping everyone informed and reducing the risk of surprises.
Define Communication Protocols
Finally, establishing clear communication protocols is essential. This includes defining who is responsible for providing updates, how often communication should occur, and what channels will be used (e.g., email, phone, TMS). By implementing these strategies, businesses can foster seamless communication, minimize errors, and ensure smooth sailing for their outbound freight.
3. Navigating Regulatory and Compliance Hurdles
Outbound shipping isn't just about getting goods from point A to point B; it's about navigating a complex web of regulations and compliance requirements. These rules, while essential for safety and fairness, can pose significant challenges for businesses. One prime example is the Hours of Service (HOS) regulations for truck drivers. These rules limit the number of hours a driver can spend behind the wheel, with mandatory rest breaks to prevent fatigue-related accidents. While crucial for safety, these regulations can impact delivery times, especially for long-haul shipments.
HOS regulations cost the trucking industry $7.7 billion annually.
Beyond HOS regulations, shippers must comply with a myriad of other rules, including weight restrictions on trucks, securement requirements for cargo, and specific protocols for transporting hazardous materials. Failing to comply can result in hefty fines, shipment delays, and even legal repercussions.
Partner with the Right Provider
So, how can businesses stay on the right side of the law and keep their freight moving smoothly? Partnering with knowledgeable logistics providers is a crucial first step. Experienced providers have a deep understanding of the regulatory landscape and can help you navigate the complexities. They can ensure your shipments comply with all applicable rules, from proper documentation to securement procedures.
Use the Right Tools
Technology also plays a vital role in compliance monitoring. Transportation Management Systems (TMS) often include features that track driver hours, monitor vehicle weight, and flag potential compliance issues. This allows you to proactively address problems and avoid the hidden costs of outbound freight.
Stay Informed
Finally, staying informed about regulatory changes is essential. The transportation industry is dynamic, with rules and regulations constantly evolving. Subscribe to industry newsletters, attend webinars, and consult with your logistics providers to stay abreast of the latest updates. By staying informed and proactive, you can ensure your outbound freight operations remain compliant and efficient.
4. Weathering the Storms: Seasonality and Disruptions
Just like the weather itself, outbound freight operations are susceptible to seasonal shifts and unexpected storms. Understanding these patterns and preparing for disruptions is crucial for maintaining a smooth flow of goods.
Seasonality plays a significant role in outbound logistics. Peak seasons, such as the holiday shopping rush or harvest time for agricultural products, create surges in demand. This can strain capacity, leading to higher transportation costs and potential delays. Imagine a toy manufacturer trying to ship its products to retailers in the weeks leading up to Christmas. The increased volume puts pressure on carriers, potentially causing shipment delays and missed deadlines.
During the 2022 holiday season, parcel carriers experienced an average of a 3% increase in delivery times.
Beyond the surge in demand during the holiday season, holidays themselves can disrupt the flow of outbound freight. For example, the Chinese New Year celebration causes a significant slowdown in export activity from China, often lasting several weeks. Factories and ports operate at reduced capacity, impacting production schedules and shipping timelines. Businesses that fail to anticipate these holiday-related interruptions may face unexpected delays and disruptions to their supply chains.
Weather-related disruptions add another layer of complexity. Severe weather events like hurricanes, blizzards, or wildfires can cause road closures, truck terminal shutdowns, and flight cancellations. These disruptions can lead to significant delays, damage to goods in transit, and increased costs. For instance, a shipment of electronics traveling through a region hit by a major snowstorm could face delays and risk damage from the extreme cold.
Proactive Planning
Proactive planning is essential to mitigate these risks. Analyze historical data to anticipate seasonal demand fluctuations and adjust your transportation strategy accordingly. Consider diversifying your carrier mix, securing capacity in advance, and exploring alternative transportation modes during peak seasons.
Weather Forecasting
Weather forecasting tools can help you anticipate potential disruptions and adjust your plans accordingly. Real-time weather updates can inform route optimization decisions, allowing you to avoid areas with severe weather conditions.
Contingency Planning
Finally, having contingency plans in place is crucial. Identify alternative routes, backup carriers, and warehousing options in case of unexpected disruptions. This preparedness can help you minimize the impact of weather-related delays and keep your supply chain moving, even in the face of stormy conditions.
Overcoming Outbound Freight Challenges
We've explored some of the most common roadblocks in outbound freight logistics. From securing reliable carriers during peak seasons to ensuring clear communication between manufacturers and drivers, these challenges can significantly impact your bottom line. Failing to address these issues can lead to delivery delays, dissatisfied customers, and increased costs.
But with the right strategies and tools, you can navigate these obstacles effectively. By proactively planning for capacity crunches, fostering open communication channels, and leveraging technology for compliance monitoring and real-time visibility, you can gain control of your outbound freight and keep your supply chain running smoothly.
Customodal offers comprehensive solutions to help you overcome these challenges and optimize your outbound freight operations. Our expertise in carrier sourcing, route optimization, and compliance management ensures efficient and cost-effective transportation.
Contact us today to learn how Customodal can help you achieve your logistics goals and drive business success!