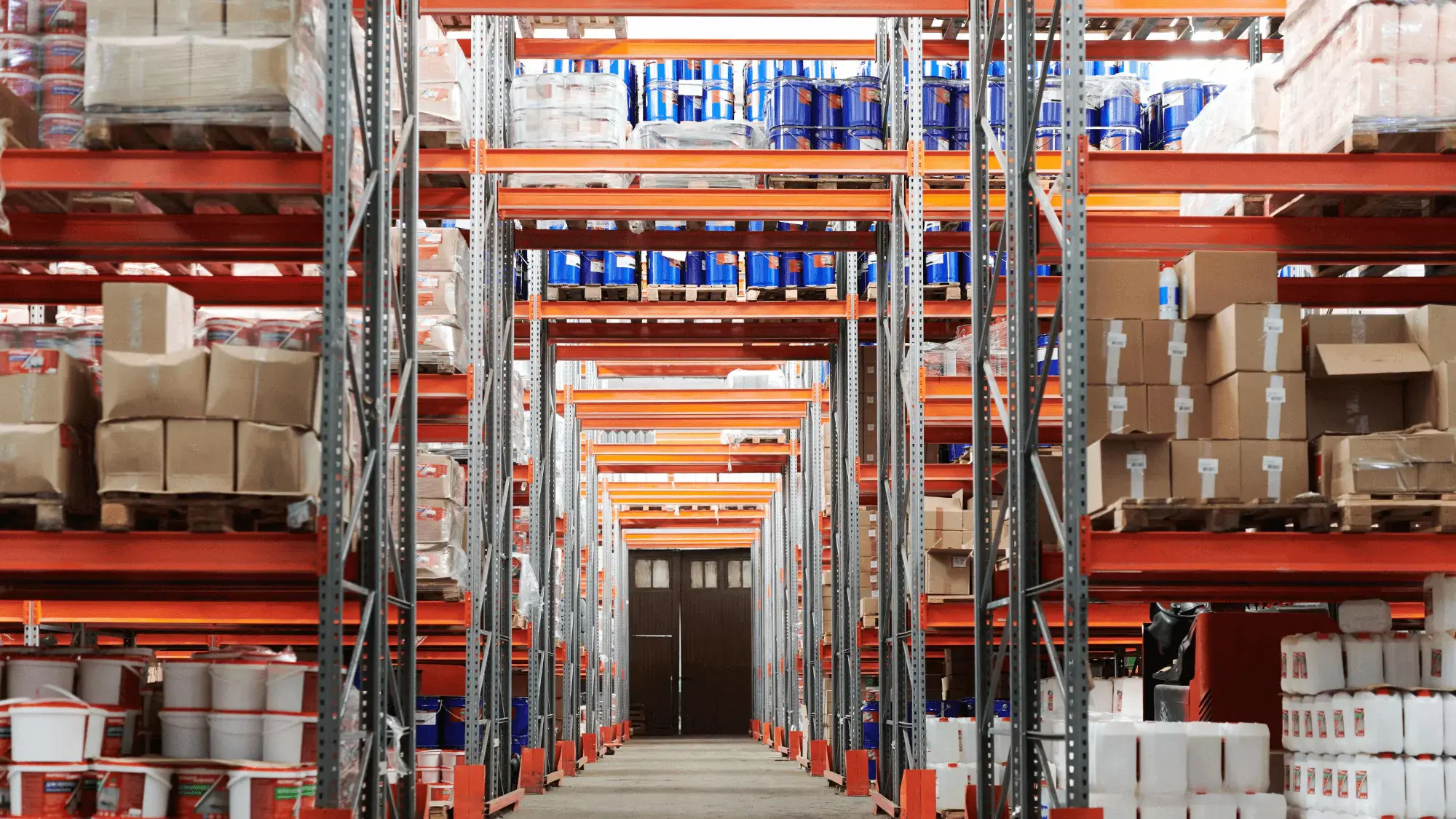
The clock is ticking. Customers want their orders yesterday, and a smooth warehouse receiving process is your secret weapon to meet those sky-high expectations. Inbound freight—the flow of goods into your facility—is essential to keep your operations running smoothly, whether you're stocking shelves with finished goods or supplying your production line with raw materials. But what happens when this process is clunky? Delays, errors, and a whole lot of frustration.
This blog post dives into proven strategies to optimize your inbound freight operations, transforming your receiving process from a bottleneck into a well-oiled machine, whether you're a distributor, manufacturer, or anything in between.
The Challenges of Inefficient Warehouse Receiving
It doesn't take much time for inefficient warehouse receiving to turn into a logistical nightmare. Imagine this: shipments pile up on the dock, paperwork goes missing, and inventory counts are constantly off. This chaotic scene isn't just frustrating—it hits your bottom line.
-
Increased receiving times: One of the most obvious consequences is increased receiving times. When goods aren't processed quickly, it creates a ripple effect, delaying putaway, order fulfillment, and, ultimately, customer delivery.
-
Inventory discrepancies: Inventory discrepancies are another major challenge. Manual data entry is prone to human error, leading to inaccurate stock counts, misplaced items, and even lost goods. These inaccuracies can result in stockouts, backorders, and dissatisfied customers.
-
Rising labor costs: These inefficiencies also drive up labor costs. More time spent searching for misplaced items, correcting errors, and reconciling inventory means more manpower is needed, increasing operational expenses.
-
Bottlenecks: The receiving area is the heart of your warehouse; any congestion here creates bottlenecks that impact the entire operation. Delays in receiving lead to delays in putaway, which slows down order fulfillment. The result? Missed delivery deadlines, increased shipping costs, and damage to your company's reputation.
-
Communication breakdowns: Communication breakdowns with carriers and suppliers further exacerbate these issues. Lack of visibility into shipment status, unclear delivery schedules, and miscommunication about delivery appointments can all contribute to receiving inefficiencies.
-
Damages and losses: Inefficient receiving increases the risk of damages and losses. Items left unattended on a crowded dock are more susceptible to damage, and poor inventory tracking makes it difficult to identify and address losses promptly.
These challenges highlight the critical need for optimized warehouse-receiving processes. By addressing these issues head-on, businesses can improve efficiency, reduce costs, and enhance customer satisfaction.
Strategies for Optimizing Warehouse Receiving Efficiency
Optimizing your warehouse receiving process requires a multi-faceted approach. Here's a breakdown of key strategies to transform your inbound freight operations:
1. Implement a Warehouse Management System
A Warehouse Management System (WMS), or WMS component of an ERP system, is the backbone of efficient receiving. This software solution automates and streamlines various processes, providing real-time visibility and control over your inventory.
-
Automated data capture and processing: Say goodbye to manual data entry and the risk of human error. A WMS automates data capture through barcode scanning, RFID tags, and other technologies, ensuring accuracy and speeding up receiving times.
-
Improved inventory visibility and tracking: Know exactly what's coming in, where it's located, and its status in real-time. This prevents discrepancies, reduces losses, and optimizes stock levels.
-
Real-time insights: A WMS provides valuable data and analytics on receiving operations, allowing you to identify bottlenecks, track key performance indicators (KPIs), and make data-driven decisions for continuous improvement.
-
Enhanced communication and collaboration: A WMS facilitates seamless communication between departments, carriers, and suppliers, ensuring everyone is on the same page.
By automating tasks and providing real-time data, a WMS empowers warehouse personnel to work more efficiently and make informed decisions. This leads to faster receiving times, reduced errors, and improved overall productivity.
2. Optimize Dock Scheduling and Management
Your receiving dock is a critical juncture in your warehouse. Inefficient dock scheduling leads to congestion, delays, and wasted resources.
-
Appointment scheduling systems: Implement a system for carriers to schedule delivery appointments, preventing docks from being overwhelmed at peak times.
-
Real-time communication: Maintain open communication with carriers regarding estimated arrival times and any potential delays. This allows for better resource allocation and minimizes waiting times.
-
Cross-docking: For fast-moving goods, consider cross-docking, where incoming shipments are directly transferred to outbound trucks without being stored in the warehouse. This speeds up turnaround times and reduces handling costs.
-
Designated receiving areas: Designate specific areas for receiving different types of goods, ensuring efficient unloading and sorting.
Effective dock scheduling ensures a smooth flow of goods in and out of the warehouse. This minimizes wait times for carriers, reduces congestion on the dock, and allows for faster processing of incoming shipments.
3. Utilize Barcode Scanning and RFID Technology
These technologies are game-changers for accurate and efficient receiving.
-
Barcode scanning: Quickly and accurately capture product information by scanning barcodes, eliminating manual data entry and reducing errors.
-
RFID technology: RFID tags provide even greater visibility, allowing for real-time tracking of goods throughout the receiving process and beyond. This is particularly useful for high-value items or those requiring special handling.
By automating data capture and improving inventory tracking, barcode scanning and RFID technology minimize errors, reduce manual effort, and enhance overall receiving efficiency.
4. Improve Communication and Collaboration
Open and timely communication with carriers and suppliers is crucial for a smooth inbound freight flow.
-
Clear communication channels: Establish preferred communication methods and protocols to ensure timely and accurate information exchange.
-
Real-time information sharing: Utilize technology to share real-time information on shipment status, delivery schedules, and any potential issues.
-
Collaborative platforms: Consider using collaborative platforms that allow for seamless information sharing and communication between all stakeholders.
-
Strong relationships: Cultivate strong relationships with your carriers and suppliers, built on trust and mutual understanding.
Effective communication fosters collaboration and trust among all parties involved in the inbound freight process. This leads to better coordination, fewer delays, and improved overall efficiency.
5. Optimize Warehouse Layout and Design
A well-designed warehouse layout can significantly impact receiving efficiency.
-
Designated receiving areas: Clearly defined receiving areas with adequate space for unloading, inspection, and sorting.
-
Clear pathways and signage: Ensure clear and unobstructed pathways for efficient movement of goods and personnel. Clear signage helps direct traffic and minimizes confusion.
-
Properly equipped workstations: Provide receiving staff with ergonomic workstations equipped with the necessary tools and technology for efficient processing.
-
Efficient space utilization: Optimize the use of space and storage solutions to maximize efficiency and minimize travel time.
A well-planned warehouse layout optimizes the flow of goods and personnel, minimizing wasted time and effort. This contributes to faster receiving times, improved productivity, and a safer working environment.
Measuring and Monitoring Warehouse Receiving Performance
You can't improve what you don't measure. Tracking key performance indicators (KPIs) provides valuable insights into the effectiveness of your warehouse receiving process. These metrics help identify areas of strength and pinpoint opportunities for improvement.
-
Receiving cycle time: This measures the time it takes to process a shipment from arrival to putaway. A shorter cycle time indicates greater efficiency.
-
Inventory accuracy rate: This measures the accuracy of your inventory data. A high accuracy rate means fewer discrepancies and stockouts.
-
Cost per line item received: This KPI tracks the cost of processing each individual item received. Lowering this cost contributes to greater profitability.
-
Dock turnaround time: This measures the time it takes for a truck to be unloaded and released from the dock. Faster turnaround times improve dock efficiency and carrier satisfaction.
-
Number of receiving errors: Tracking the number of errors, such as incorrect counts or misidentified items, helps pinpoint areas where processes need to be tightened.
By analyzing these KPIs, you gain a clear understanding of your warehouse receiving performance. This data allows you to identify bottlenecks, assess the impact of process changes, and track progress over time. Regular monitoring and analysis of KPIs enable data-driven decision-making, leading to continuous improvement and optimized warehouse operations.
Unlocking Efficiency: Your Path to Streamlined Warehouse Receiving
Efficient warehouse receiving is the cornerstone of a successful supply chain. By optimizing this crucial process, businesses can unlock significant improvements in productivity, accuracy, and cost-effectiveness. Implementing a robust WMS, streamlining dock scheduling, leveraging technology, and fostering clear communication are key steps toward achieving warehouse receiving excellence.
Customodal offers a comprehensive suite of solutions designed to optimize your inbound freight operations. Our platform seamlessly integrates with leading WMS systems, providing real-time visibility and control over your inventory. Our advanced dock scheduling capabilities help minimize wait times and maximize throughput. And with our real-time tracking and communication tools, you can stay connected with carriers and suppliers every step of the way.
Ready to transform your warehouse receiving process? Partner with Customodal as your 3PL in freight logistics! Contact us today for a free consultation and discover how you can optimize your inbound freight.