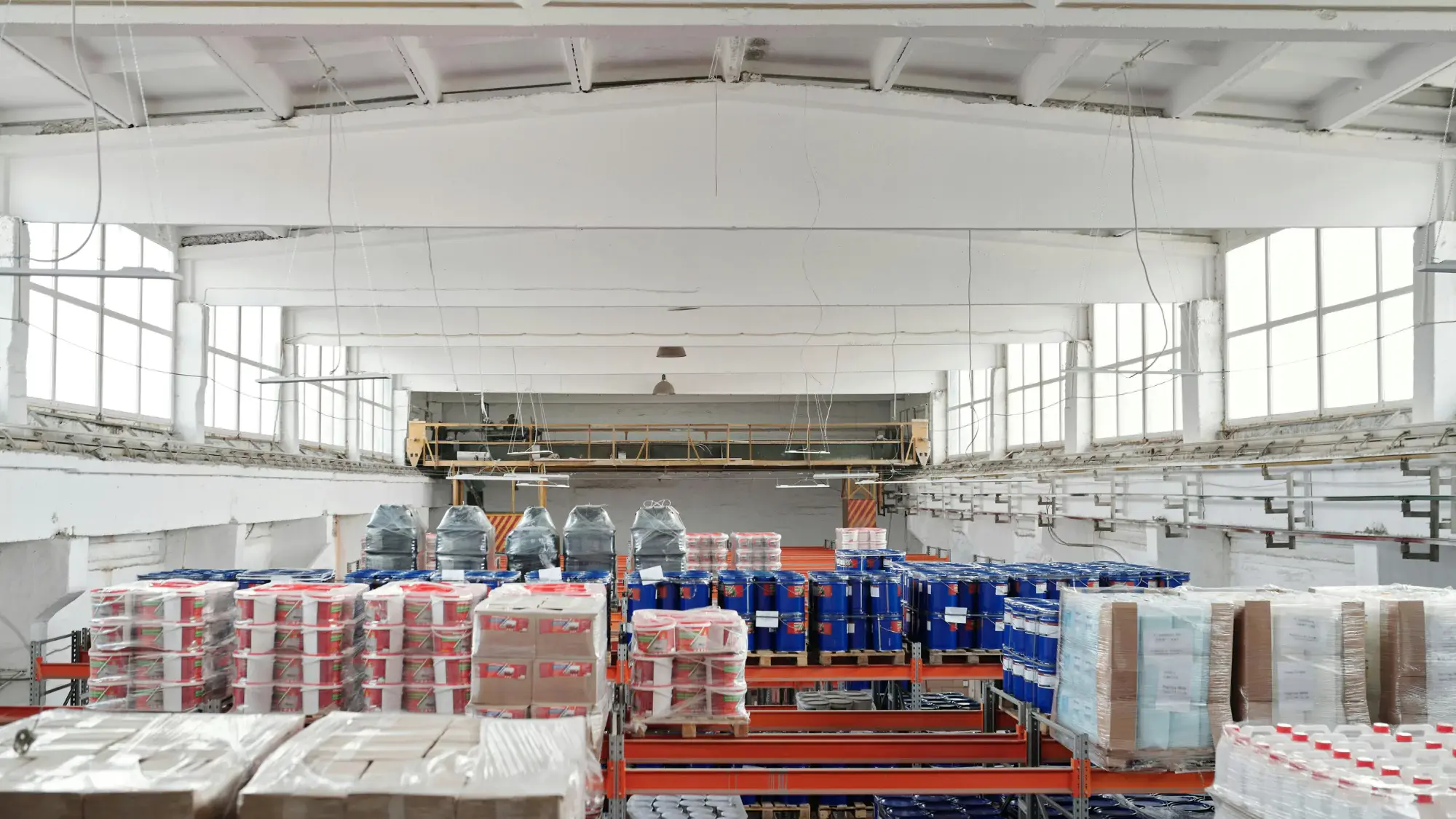
Inbound logistics–it's the lifeblood of your supply chain, responsible for the flow of goods into your business. But are you receiving, storing, and distributing these goods as efficiently as possible? How do your operations measure up?
Benchmarking provides the answer; by analyzing KPIs and comparing your performance to industry standards, you can gain valuable insights into your strengths and weaknesses.
KPIs in Inbound Logistics
Are you looking for the secrets to inbound freight logistics success? The answer lies in something you already have–the numbers. Key Performance Indicators (KPIs) are the keys to understanding how your operations are truly performing. They provide a clear picture of your strengths and weaknesses, enabling you to make data-driven decisions that boost efficiency and drive bottom-line results.
Here are the essential inbound logistics KPIs you should be tracking if you aren't already:
Receiving Efficiency
This KPI focuses on the speed and accuracy of receiving incoming goods. It includes metrics such as:
-
Time to unload: How long does it take to unload a shipment?
-
Cost per shipment received: What are the costs associated with processing each incoming shipment?
-
Receiving cycle time: How long does it take to process a shipment from arrival to storage?
-
Receiving accuracy: Are you receiving the correct goods and quantities
Inventory Management
Efficient inventory management is crucial for minimizing holding costs and preventing stockouts. Key metrics include:
-
Inventory turnover rate: How quickly is your inventory sold and replenished?
-
Carrying costs: What are the costs associated with storing inventory (e.g., storage space, insurance, obsolescence)?
-
Order fulfillment accuracy: Are you shipping the correct products to customers?
-
Inventory accuracy: Does your physical inventory match your records?
Transportation Costs
This KPI focuses on optimizing transportation expenses. Consider these metrics:
-
Cost per mile: What is the cost of transporting goods per mile?
-
Cost per shipment: What are the costs associated with each shipment?
-
Fuel efficiency: Are you using fuel-efficient transportation methods?
-
Transportation time: How long does it take to transport goods from suppliers to your warehouse?
Supplier Performance
Your suppliers play a crucial role in the success of your inbound logistics. Track these metrics:
-
On-time delivery rate: How often do suppliers deliver on time?
-
Lead time variability: How consistent are supplier lead times?
-
Order accuracy: How often do suppliers deliver the correct goods and quantities?
-
Supplier defect rate: What is the percentage of defective goods received from suppliers?
Order Cycle Time
This KPI measures the total time it takes to complete an order, from placement to delivery. A shorter order cycle time generally indicates greater efficiency. It includes aspects such as:
-
Order processing time: How long does it take to process an order internally?
-
Supplier lead time: How long does it take for the supplier to deliver the goods?
-
Delivery time: How long does it take to deliver the goods to their final destination?
These KPIs offer a powerful lens through which you can magnify the inner workings of your inbound logistics. But simply tracking them isn't enough. To truly harness their potential, you need to analyze the data, identify trends, and pinpoint areas for improvement.
For example, if your "time to unload" metric is consistently high, it might indicate a need for process improvements in your receiving area, such as implementing cross-docking or investing in warehouse management systems.
Similarly, a low "inventory turnover rate" could signal overstocking or issues with demand forecasting, requiring adjustments to your inventory management strategies. By actively using these KPIs to guide your decisions, you can transform your inbound logistics from a cost center into a source of competitive advantage.
Inbound Logistics Benchmarks for Peak Performance
Understanding your own inbound logistics KPIs is a crucial first step, but how do you know if your performance is truly top-notch? This is where industry benchmarks come into play. Benchmarking involves comparing your key metrics against averages or best-in-class performance within your industry. It provides a valuable yardstick for measuring your competitiveness and identifying areas for improvement.
While specific benchmark data will vary depending on your industry and other factors, here are some general benchmarks for the KPIs we discussed earlier, based on recent industry research and reports:
-
Receiving efficiency: According to a 2023 study by Aberdeen Research, best-in-class companies aim for a receiving cycle time of under 60 minutes. This includes the time it takes to unload the shipment, inspect the goods, and move them to storage.
-
Inventory management: The average inventory turnover rate for the manufacturing industry in 2024 is 8.5, according to the APICS Dictionary. However, this can vary significantly depending on the specific sector. For example, the food and beverage industry typically has a much higher turnover rate due to perishability.
-
Transportation costs: A report by the Council of Supply Chain Management Professionals (CSCMP) found that transportation costs for most businesses should ideally be between 4% and 10% of total revenue. Companies exceeding this range may need to explore strategies for cost optimization, such as route optimization, carrier negotiations, or alternative transportation modes.
-
Supplier performance: Industry leaders achieve an on-time delivery rate of 96% or higher, according to a 2024 survey by Supply Chain Insights. This highlights the importance of strong supplier relationships and effective communication to ensure timely deliveries.
-
Order cycle time: Logistics Management reports that leading companies in the ecommerce sector are achieving an average order cycle time of 1-2 days for domestic shipments. This requires streamlined order processing, efficient warehouse operations, and fast delivery methods.
Note: It's important to remember that these are just general guidelines. Several factors can influence these benchmarks, including:
-
Industry: Different industries have different standards. For example, perishable goods will have a much faster inventory turnover rate than durable goods.
-
Company Size: Larger companies often have more resources and leverage to achieve better economies of scale.
-
Geographic Location: Transportation costs and delivery times can be significantly affected by location and proximity to suppliers.
By analyzing benchmark data, you can gain valuable insights into your company's performance. For example, if your on-time delivery rate is significantly lower than the industry average, it may indicate a need to improve supplier relationships or explore alternative transportation options. Conversely, if your inventory turnover rate is higher than the benchmark, it could suggest that your inventory management practices are highly efficient.
Benchmarking provides a roadmap for continuous improvement, helping you identify areas where you excel and those where you need to catch up to–or even surpass–the competition.
Fueling Efficiency: Strategies to Optimize Your Inbound Logistics
Now that you have a grasp of essential KPIs and industry benchmarks, it's time to put that knowledge into action. Here are some practical steps you can take to optimize your inbound logistics performance:
-
Streamline receiving processes: Implement cross-docking to transfer goods directly from incoming to outbound transportation, reducing storage time and handling costs. Invest in a Warehouse Management System (WMS) to automate tasks, improve accuracy, and gain real-time visibility into inventory levels.
-
Optimize inventory management: Adopt Just-in-Time (JIT) inventory practices to minimize storage costs and reduce the risk of obsolescence. Leverage demand forecasting techniques to accurately predict inventory needs and avoid stockouts.
-
Reduce transportation costs: Negotiate favorable rates with carriers by leveraging your shipment volume. Explore alternative transportation modes like rail or intermodal to optimize costs based on distance and shipment size. Implement route optimization software to minimize mileage and fuel consumption.
-
Strengthen supplier relationships: Establish clear communication channels with suppliers to ensure alignment and address potential issues proactively. Collaborate on forecasting and planning to improve on-time delivery rates and reduce lead time variability.
-
Embrace technology: Leverage freight tech like Transportation Management Systems (TMS) to gain visibility into shipments, optimize routes, and manage carriers effectively. Explore warehouse automation technologies like automated guided vehicles (AGVs) and robotics to improve efficiency and reduce labor costs. Utilize data analytics to identify trends, predict potential disruptions, and make data-driven decisions.
Transform Your Business with Smarter Logistics
By implementing these strategies, you can transform your inbound logistics operations into a well-oiled machine, driving efficiency, reducing costs, and improving customer satisfaction. Need help getting started? Customodal offers comprehensive logistics solutions tailored to your specific needs.
Contact Customodal today to learn more about how we can help you achieve inbound logistics excellence!