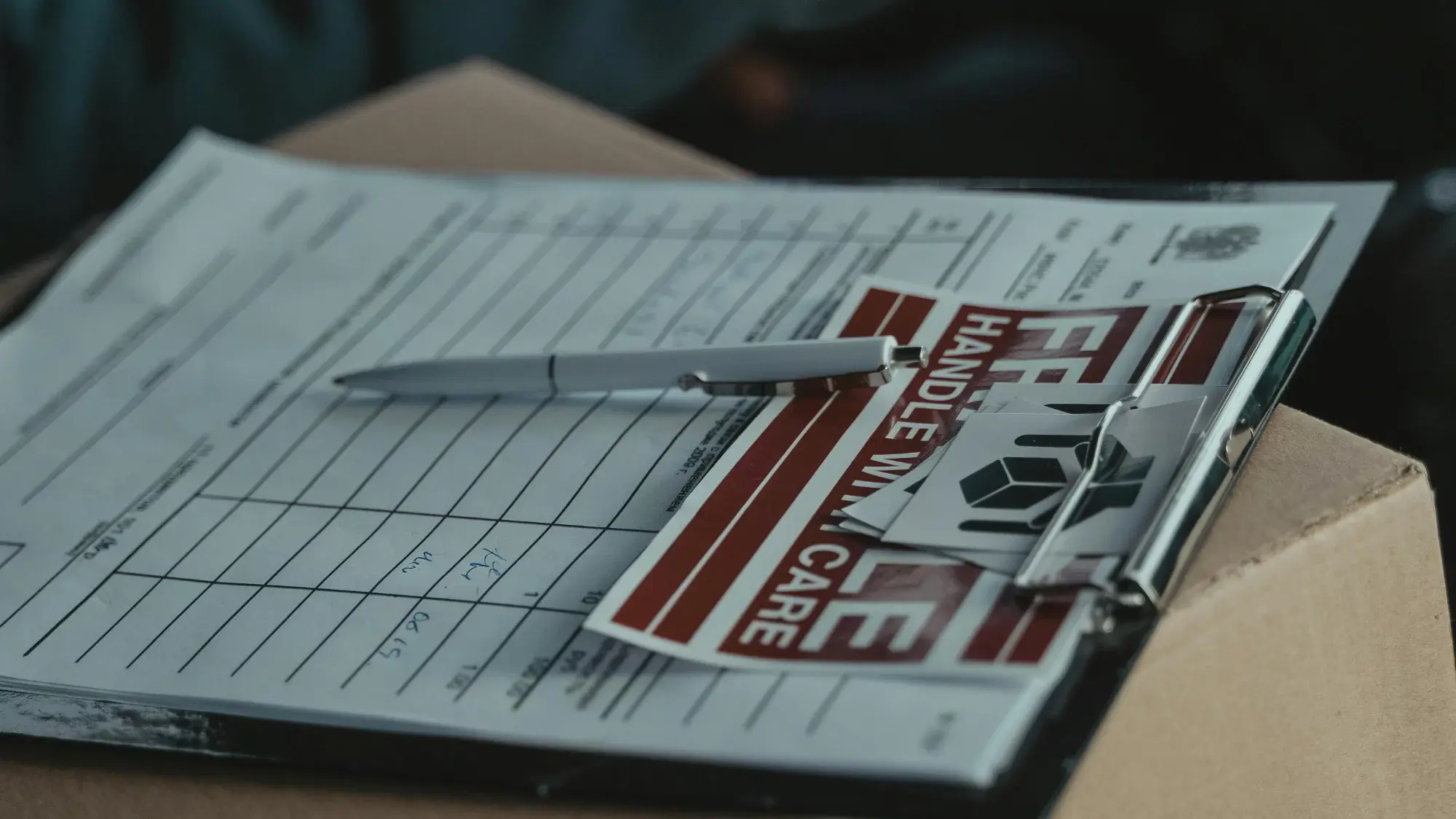
That moment of arrival can be filled with anticipation–the unloading, the inventory checks, the final step in your supply chain. But what happens when that expectation is met with the unwelcome sight of damaged goods? Discovering compromised freight can trigger a cascade of concerns, from immediate replacement costs to potential delays and dissatisfied customers. When it happens, the occurrence of freight damage can be significant.
So, how can businesses navigate these challenges effectively? Understanding both how to prevent freight damage and how to efficiently manage the claims process when it does occur is crucial.
The Underestimated Costs of Damaged Freight
While the immediate expense of replacing damaged goods is a tangible hit to your bottom line, the true cost of freight damage extends far beyond this initial outlay. Consider the lost sales opportunities that arise when promised inventory fails to arrive in sellable condition. Production schedules can be thrown into disarray, leading to missed deadlines and potential penalties. The time and resources spent on investigating the damage, processing paperwork, and communicating with all parties involved create a significant administrative burden, diverting valuable employee time from core business activities.
Perhaps even more critical in the long term is the potential damage to customer relationships and your brand's reputation. In today's competitive market, a consistent and reliable delivery experience is paramount. Receiving damaged goods can lead to customer dissatisfaction, returns, negative reviews, and ultimately, the loss of valuable business. Packaging Digest estimates that as many as 11% of loads arrive with some kind of damage, with the average sitting at about 2%.
Consider a scenario where a shipment of perishable food items is transported in the same trailer as improperly secured hazardous materials. Even if the food packaging remains physically intact upon arrival, the potential for contamination renders the entire shipment unusable. If this issue is caught during receiving inspection, the company faces a complete loss of that inventory.
However, if the contamination isn't immediately apparent and the food reaches consumers, the consequences could be far more severe, leading to recalls, significant reputational damage, and potential legal liabilities. This example starkly illustrates how indirect damage, stemming from improper handling or co-loading, can lead to substantial monetary losses and jeopardize brand trust.
Proactive Measures: Shielding Your Shipments from Damage
While the claims process is a necessary safeguard, the most effective strategy for mitigating the costs and headaches associated with freight damage lies in proactive prevention. Implementing robust measures before your goods even leave the loading dock can significantly reduce the likelihood of damage occurring in the first place. Think of it as building a strong defense for your valuable shipments.
Proper Packaging Standards
-
Match packaging strength to the mode of transport and the fragility of the goods.
-
Utilize appropriate cushioning materials (void fill, bubble wrap, foam).
-
Consider ISTA (International Safe Transit Association) testing as a benchmark for packaging integrity.
Secure Palletizing Techniques
-
Employ proper stacking patterns for load stability.
-
Use effective stretch wrap and banding to secure the load.
-
Incorporate edge protectors and top sheets for added protection.
Selecting Reliable Carriers
-
Prioritize carriers with a strong track record for safe handling.
-
Consider carriers specializing in your freight type for their expertise.
Clear and Accurate Labeling
-
Ensure labels are securely attached and easily legible.
-
Use handling instructions (e.g., "Fragile," "This Side Up") when necessary.
-
Provide accurate weight and dimension information for proper handling and loading.
Shipping Insurance
-
Consider supplemental all-risk cargo insurance for broader coverage.
-
Benefit from a potentially simplified claims process with faster payouts.
-
Gain coverage for situations where standard carrier liability may not apply.
-
View this as a valuable investment for enhanced peace of mind and financial security.
By focusing on these proactive measures, you can significantly reduce the incidence of freight damage and protect your valuable goods.
Freight Claims: What Happens When Damage Occurs?
Despite implementing the most diligent preventative measures, the reality of freight shipping is that damage can still occur. When faced with this situation, understanding the claims process is crucial for a swift and potentially favorable resolution. Navigating this process might seem daunting, but breaking it down into key steps can provide clarity and empower you to take the necessary actions.
Immediate Action Upon Discovery
Upon receiving a shipment, a thorough inspection is paramount. If you observe any signs of damage, such as crushed boxes, torn wrapping, or visible leaks, it's critical to document everything meticulously before signing the delivery receipt. Make detailed notes of the damage directly on the receipt, and if possible, take clear photographs and videos as visual evidence. Retain the damaged goods and all original packaging materials, as these may be required for carrier inspection.
Gather Critical Data
A successful claim hinges on providing comprehensive documentation. The Bill of Lading (BOL) serves as the fundamental contract of carriage, outlining the details of the shipment, including the goods, origin, and destination. You will also need to provide proof of the shipment's value, such as the original invoice or purchase order.
A detailed inspection report, separate from the notes on the delivery receipt, should clearly describe the nature and extent of the damage. Supplement this report with the photographs and videos taken upon discovery, as these provide irrefutable visual evidence.
Understand Carrier Liability
It's important to understand the concept of carrier liability, which dictates the carrier's responsibility for loss or damage during transit. However, carrier liability is not absolute and often has limitations.
For Less-Than-Truckload (LTL) shipments, liability is commonly limited to a certain dollar amount per pound. Additionally, there are exclusions to carrier liability. For instance, damage resulting from improper packaging by the shipper is often not the carrier's responsibility. Understanding these limitations is crucial for setting realistic expectations for claim recovery.
File the Claim
Each carrier has its own specific procedures and deadlines for filing claims. It is essential to obtain this information promptly and adhere to it strictly. Typically, this involves completing a claim form provided by the carrier and submitting all the gathered documentation. Accuracy and timeliness are paramount to ensure your claim is processed efficiently. Submitting incomplete or late documentation can lead to delays or even the denial of your claim.
Your Ally in the Claims Process: How Your 3PL Steps In
Navigating the complexities of a freight damage claim can be a time-consuming and frustrating endeavor, often pulling valuable resources away from your core business operations. This is where the strategic partnership with a third-party logistics provider (3PL) can prove to be an invaluable asset, offering specific expertise to streamline the entire procedure.
A knowledgeable 3PL brings a deep understanding of carrier liability. They can help you decipher the often-intricate terms and conditions, ensuring you understand the carrier's responsibilities and limitations in specific damage scenarios. For instance, they can advise on situations where carrier liability might be limited due to packaging issues or specific commodity types.
Furthermore, a proactive 3PL often vets carriers rigorously. Their established relationships and performance monitoring allow them to select partners with strong track records for careful handling, potentially reducing the incidence of damage in the first place. In the unfortunate event of damage, this pre-existing knowledge of the carrier's processes can expedite the claims communication.
Another critical area where a 3PL provides expertise is in understanding proper loading and co-loading practices. They can advise on how shipments should be correctly loaded and secured to minimize the risk of damage during transit. By leveraging a 3PL's knowledge and experience, businesses can significantly simplify the often-challenging process of freight damage claims.
Partnering for Seamless Claims Resolution
Dealing with the aftermath of damaged freight doesn't have to be a solitary and stressful undertaking. At Customodal, we recognize the disruptions and financial implications that damaged shipments can cause. Our experienced team is committed to providing thorough support throughout the claims journey. We offer guidance in compiling necessary documentation, streamline the claim filing process, and actively represent your interests to achieve a prompt and equitable resolution.
Seeking a logistics partner dedicated to your success and providing robust claims assistance? Contact Customodal today to discover how we can optimize your supply chain and offer the support you deserve.